Düngemittel aus der Luft gegriffen
Im September 1913 ging bei der BASF in Ludwigshafen die erste Produktionsanlage zur industriellen Synthese von Ammoniak in Betrieb
Auch 100 Jahre nach dem Beginn der industriellen Produktion der Grundchemikalie Ammoniak ist ein Besuch der beiden Ammoniakfabriken der BASF in Ludwigshafen beeindruckend. Wenn man vor dem etwa 20 Meter hohen Reaktor der älteren Anlage steht und an die elementaren Urgewalten denkt, mit denen darin Stickstoff und Wasserstoff zu Ammoniak reagieren, erfasst man die Bedeutung dieses wissenschaftlich-technischen Durchbruchs. Das Haber-Bosch-Verfahren zur Ammoniaksynthese, das hier im September 1913 erstmals erfolgreich umgesetzt wurde, war der entscheidende Schritt ins Zeitalter der Mineraldünger. Es bildete eine wichtige Grundlage für die Entwicklung der Industriegesellschaft und sichert bis heute die Ernährung von Milliarden Menschen. Der Hochdruckreaktor vor uns ist ein Urenkel des von Carl Bosch entwickelten Apparates, deutlich größer zwar, aber von ähnlicher Gestalt. Nebenan, in der neueren Anlage, lässt die weiterentwickelte Verfahrenstechnik weniger sichtbare historische Parallelen zu. Die beiden Ammoniak-Fabriken zusammen produzieren pro Tag mehr als 2.000 Tonnen der begehrten Verbindung NH3.
„Die Realisierung der industriellen Ammoniaksynthese war mit hohen unternehmerischen Risiken verbunden und erforderte viel Durchhaltevermögen“, betont der Produktionsleiter Michael Mauß. „Verfahren und Apparate für diese bahnbrechende Technologie mussten von Grund auf neu entwickelt werden.“
Die Grundlagen zur „Synthese von Ammoniak aus dessen Elementen“ legte Professor Fritz Haber ab 1904 mit seinen Arbeiten an der Technischen Hochschule Karlsruhe. Die großtechnische Umsetzung der Ammoniaksynthese, mit der die BASF 1909 Carl Bosch betraute, brachte dann zunächst ungeahnte Probleme mit sich. Denn das Hochdruckverfahren erforderte Drücke und Temperaturen, die das bisher technisch Übliche erheblich überstiegen. Dem hielten die ersten Apparaturen nicht stand, ihre Stahlreaktoren zerbarsten. Der in Metallurgie erfahrene Chemiker Bosch stieß beim genauen Studium der verwendeten Metalle schließlich auf die Ursache: Der heiße, unter hohem Druck stehende Wasserstoff löste den für die Festigkeit maßgeblichen Kohlenstoff aus den Stahlwänden, die dadurch weich und gleichzeitig spröde wurden. Bosch meisterte die Aufgabe, indem er die Apparate innen mit einem dünnen, kohlenstoffarmen Weicheisenfutter auskleidete und Löcher in die drucktragende Stahlwand bohrte. So konnte der in den Werkstoff eingedrungene Wasserstoff nach außen entweichen, ohne Schäden anzurichten. Für die innovative Hochdrucktechnik brauchte man weitere Bauteile, die nirgendwo erhältlich waren, also selbst konstruiert und getestet werden mussten. Deshalb gründete die BASF 1912 den ersten Materialprüfbetrieb der chemischen Industrie.
„Auch heute noch fahren wir bei der industriellen Produktion von Ammoniak an der Grenze des Möglichen. Die Herausforderungen an Material und Technik der Produktionsanlage sind bei diesen Hochdrucksynthesen enorm“, zieht Dr. Jürgen Korkhaus, der Leiter der Werkstofftechnik, die Parallele zur Gegenwart. „Schon kleine Schwankungen im Prozess können eine große Materialbelastung bedeuten. Deshalb müssen Auslegung und Verarbeitung der eingesetzten Apparate äußerst sorgfältig erfolgen.“ Der Reaktor der neueren Ammoniakfabrik, in dem das Synthesegasgemisch über einem Katalysatorbett bei mehr als 400 Grad Celsius und mehr als 150 Bar Druck zu Ammoniak reagiert, besitzt eine 15 Zentimeter dicke Wand aus einem hochfesten Stahl. Dessen weiterentwickelte Legierung widersteht dem Druckwasserstoff, so dass das legendäre Futterrohr heute verzichtbar ist.
Auch der Rohstoff für die Erzeugung des Synthesegases ist heute ein anderer: In den ersten Dekaden des Haber-Bosch-Verfahrens bereiteten die zahlreichen Mitarbeiter ein Bett aus glühendem Koks und leiteten Wasserdampf darüber. Heute nutzen die Ammoniakfabriken Erdgas als Rohstoff und Energieträger, das damit auch den Löwenanteil der Produktionskosten ausmacht. Am Standort Ludwigshafen ist die Ammoniakproduktion der zweitgrößte Erdgasverbraucher – nach den werkseigenen Kraftwerken. Der benötigte Stickstoff stammt wie damals aus der zugeführten Luft und ist ausnahmsweise kostenlos zu haben.
Die industrielle Synthese der Grundchemikalie Ammoniak ist längst zum unverzichtbaren Bestandteil des Produktionsverbundes geworden. Bei BASF in Ludwigshafen werden daraus heute vor allem Leime und Tränkharze auf Harnstoffbasis für Holzwerkstoffe hergestellt, aber auch verschiedene Amine und Caprolactam, der Ausgangsstoff für Polyamid-Kunststoffe. Weltweit dagegen gehen nach wie vor gut drei Viertel des erzeugten Ammoniaks in die Produktion von Düngemitteln.
Weitere News aus dem Ressort Wirtschaft & Finanzen
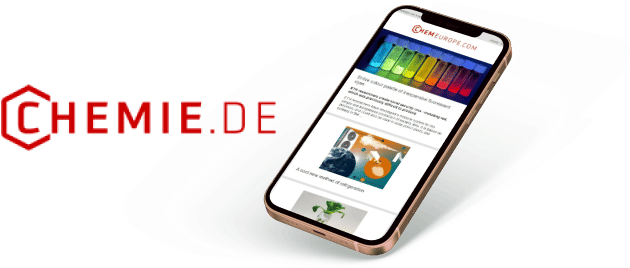
Holen Sie sich die Chemie-Branche in Ihren Posteingang
Mit dem Absenden des Formulars willigen Sie ein, dass Ihnen die LUMITOS AG den oder die oben ausgewählten Newsletter per E-Mail zusendet. Ihre Daten werden nicht an Dritte weitergegeben. Die Speicherung und Verarbeitung Ihrer Daten durch die LUMITOS AG erfolgt auf Basis unserer Datenschutzerklärung. LUMITOS darf Sie zum Zwecke der Werbung oder der Markt- und Meinungsforschung per E-Mail kontaktieren. Ihre Einwilligung können Sie jederzeit ohne Angabe von Gründen gegenüber der LUMITOS AG, Ernst-Augustin-Str. 2, 12489 Berlin oder per E-Mail unter widerruf@lumitos.com mit Wirkung für die Zukunft widerrufen. Zudem ist in jeder E-Mail ein Link zur Abbestellung des entsprechenden Newsletters enthalten.
Meistgelesene News
Weitere News von unseren anderen Portalen
Zuletzt betrachtete Inhalte
