Ultramid - the missing link
Das Polyamid der BASF findet Einsatz im Drosselklappengehäuse
Zusammen mit der BASF gelang es dem französischen Automobilhersteller MGI Coutier Drosselsysteme aus Polyamid zu entwickeln.
In modernen Automobilen sind im Laufe der letzten drei Jahrzehnte zahlreiche, ehemals aus Metall bestehende Bauteile durch Kunststoffteile ersetzt worden, nicht nur unter der Motorhaube. Besonders im Luftansaugtrakt hat sich die BASF durch die Entwicklung des Ansaugrohrs aus Kunststoff seit 1972 einen Namen gemacht. Und dazu beigetragen, dass heute fast alle Teile des Luftansaugtrakts aus Kunststoffen - vornehmlich aus Polyamid - gefertigt werden; dazu gehören Luftführungen, Luftfiltergehäuse, Resonatoren, Luftmassenmesser-Gehäuse und natürlich die Ansauganlage. Das fehlende Glied in dieser Kette war bisher die Luftmassensteuerung, das Drosselklappengehäuse.
MGI Coutier, Automobilzulieferer aus Champfromier/Frankreich, hat nun in Zusammenarbeit mit den Ingenieuren der BASF-Geschäftseinheit Engineering Plastics Europe zwei Drosselklappen aus Ultramid®, dem Polyamid der BASF, entwickelt. Ultramid A3WG6, ein Polyamid 66 mit 30 Prozent Glasfasern, kommt bei Renaults 1,4- Liter-E7J-Motor im Clio, Megane und Kangoo zum Einsatz. Die Polyamid-Variante mit 35 Prozent Glasfaseranteil, das Ultramid A3WG7, wird bei den PSA 1.7/2.0 Liter EW- Motoren von Peugeots 307, 406, 607 , in den Citroëns Xantia / Xsara und im neuen C5 verwendet. In beiden Fällen handelt es sich um einen mechanischen Drosselklappensteller. MGI Coutier S.A. ist als Tier-One-Supplier Direktlieferant von Renault, PSA, Ford, VW, GM und Fiat.
Ultramid ist beständig gegenüber mechanischen Belastungen ebenso wie gegenüber den im Motorraum üblichen Betriebsmitteln. Das anspruchsvolle Design des Hybridbauteils stellt außerdem sicher, dass die hohen Anforderungen an die Leckluftrate erfüllt werden: Der spezifizierte Temperaturbereich geht von -40 bis +140 Grad Celsius.
Die besonderen Vorteile des Kunststoffbauteils im Vergleich zu seinem Vorgänger aus Aluminium sind Gewichtsreduzierung, Kosteneinsparung und höhere Gestaltungsfreiheit. Durch das geringere Gewicht verringern sich die Massenkräfte und das Vibrationsverhalten wird verbessert. Gegenüber der Aluminiumausführung werden bis zu 50 Prozent Gewicht eingespart. Da ehemals separate Gehäuseteile in das Bauteil integriert werden, reduzieren sich Montageaufwand und Herstellkosten. Und schließlich kann der Designer aus Kunststoff komplexere Formen entwickeln als aus Metall. Bei der Drosselklappe führt das zu einem erheblich flexibleren Regelverhalten.
Darüber hinaus ergibt sich durch die Verwendung des Standardkunststoffs Polyamid im Drosselsystem Potential für zukünftige Entwicklungen: Das Bauteil wird sich direkt in das - ebenfalls aus Polyamid bestehende - Luftansaugmodul integrieren lassen.
Weitere News aus dem Ressort Forschung & Entwicklung
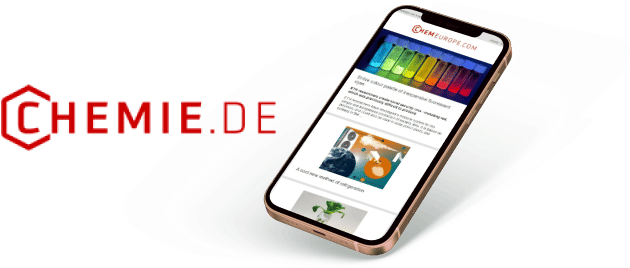
Holen Sie sich die Chemie-Branche in Ihren Posteingang
Mit dem Absenden des Formulars willigen Sie ein, dass Ihnen die LUMITOS AG den oder die oben ausgewählten Newsletter per E-Mail zusendet. Ihre Daten werden nicht an Dritte weitergegeben. Die Speicherung und Verarbeitung Ihrer Daten durch die LUMITOS AG erfolgt auf Basis unserer Datenschutzerklärung. LUMITOS darf Sie zum Zwecke der Werbung oder der Markt- und Meinungsforschung per E-Mail kontaktieren. Ihre Einwilligung können Sie jederzeit ohne Angabe von Gründen gegenüber der LUMITOS AG, Ernst-Augustin-Str. 2, 12489 Berlin oder per E-Mail unter widerruf@lumitos.com mit Wirkung für die Zukunft widerrufen. Zudem ist in jeder E-Mail ein Link zur Abbestellung des entsprechenden Newsletters enthalten.