Umweltfreundliche Pulverlacke konkurrenzfähig machen
Die ökologischen Vorteile von Pulverlacken gegenüber konventionellen Lacksystemen sind unbestritten. Sie werden lösungsmittel- und damit emissionsfrei aufgebracht. Overspray (Lackpartikel, die nicht auf dem zu lackierenden Substrat auftreffen) wird zurückgewonnen und wiederverwendet. Damit lassen sich nahezu 100% der Pulverlacksubstanz ausnutzen. Limitiert ist eine Anwendung der Pulverlacktechnologie bisher dadurch, dass der Lackierprozess mit Pulverlacken bei deutlich höheren Einbrenntemperaturen abläuft. So vernetzen wetterstabile, thermisch härtende Pulverlacke in der Regel bei Temperaturen über 160°C. Bei diesen Temperaturen können nicht wärmebeständige Substrate (Holz, Kunststoffe), aber auch metallische Legierungen mit speziellen Eigenschaften bisher nicht beschichtet werden.
Innerhalb des vom Bundesministerium für Bildung und Forschung geförderten Programms "Integrierter Umweltschutz in der Kunststoff- und Kautschukindustrie" arbeiten Wissenschaftler des Leibniz-Instituts für Polymerforschung Dresden gemeinsam mit Projektpartnern aus der chemischen Industrie (u. a. Degussa AG, Akzo), anderen Forschungseinrichtungen (u. a. Fraunhofer IWU Chemnitz, HTW Dresden) und potenziellen Anwendern (u. a. Daimler Chrysler) an der Entwicklung innovativer Pulverlacke und Verarbeitungstechnologien, die diese Nachteile abbauen und die Pulverlacktechnologie in neuen Anwendungsbereichen konkurrenzfähig machen.
Derzeit werden in zahlreichen Leichtbauanwendungen Aluminiumbleche zunächst zu Bauteilen umgeformt, auf die nachfolgend der Lack aufgebracht und ausgehärtet wird. Um eine gute Lackhaftung zu realisieren, sind durch Umformprozesse bedingte Hilfsstoffe auf der Metalloberfläche, wie Fette und Öle, in zeit- und kostenintensiven Reinigungs- und Beizoperationen vor der Beschichtung vollständig zu entfernen. Angestrebt ist nun nichts weniger als eine komplette Umkehr des technologischen Prozesses zur Herstellung von vorlackierten Metallbauteilen. Nach erfolgreichem Abschluss des Forschungsprojektes wird es möglich sein, die Pulverlackierung und Aushärtung an Blechen und Bandmaterial vorzunehmen und diese erst nachträglich umzuformen. Dadurch werden nicht nur Lackierstrecken bei den Anwendern überflüssig, es entfallen auch die Reinigungs- und Beizoperationen, was erheblich zu Umweltentlastung und Kosteneinsparung beiträgt. Die Herausforderung für die Forscher besteht darin, das Pulverlacksystem in chemischer und technologischer Hinsicht so zu gestalten, dass die Beschichtung dem Umformprozess ohne Qualitätsminderung standhält. Da Aluminium bei den derzeit in der Pulverlackierung erforderlichen Einbrenntemperaturen von über 160 °C versprödet, sind Lacksysteme mit Härtungstemperaturen unter 150 °C erforderlich, die nach dem Einbrennen einen flexiblen und damit umformbeständigen Film bilden.
Am Leibniz-Institut für Polymerforschung Dresden wurde in den vergangenen Jahren ein neues Katalysatorsystem entwickelt, dass für qualitativ hochwertige Polyurethanbeschichtungen auf Basis abspaltfreier Uretdionvernetzer Einbrenntemperaturen zwischen 120-150°C ermöglicht. Grundlagenuntersuchungen zum Reaktionsmechanismus haben darüber hinaus gezeigt, dass die Vernetzung in Gegenwart dieser Katalysatoren nach einem bisher nicht beschriebenen Mechanismus in Polymerschmelzen erfolgt.
Bis zum gegenwärtigen Bearbeitungszeitpunkt wurden Pulverlackrezepturen entwickelt, die bezüglich der resultierenden mechanischen Eigenschaften schon voll den Anforderungen der potenziellen Anwender entsprechen. Durch Optimierung der chemisch reaktiven Bestandteile (Harz, Vernetzer) sowie der Pulverlackrezeptur sollen künftig auch glatte und hochglänzende Lackschichten realisierbar sein.
Weitere News aus dem Ressort Wissenschaft
Diese Produkte könnten Sie interessieren
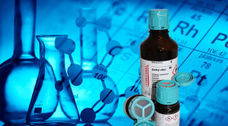
ERBAdry von CARLO ERBA Reagents
Wasserfreie Lösungsmittel von CARLO ERBA Reagents im cleveren Redesign
ERBAdry-Serie begeistert durch neueste Generation von Septen und Verschlusskappen
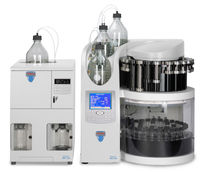
Thermo Scientific™ Dionex™ ASE™ 150 oder 350 Accelerated Solvent Extractor Systeme von Thermo Fisher Scientific
Accelerated Solvent Extraction (ASE) - die beste Probenvorbereitung für die GC und LC
Beschleunigte Lösemittelextraktion - bessere Extraktionen, schneller und mit weniger Lösemittel
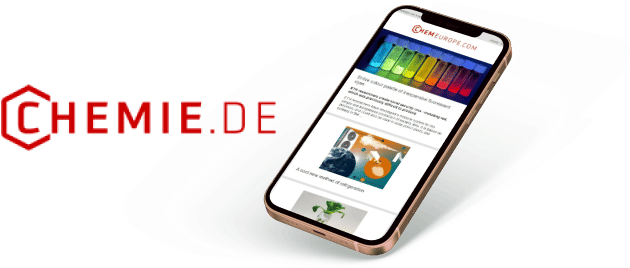
Holen Sie sich die Chemie-Branche in Ihren Posteingang
Mit dem Absenden des Formulars willigen Sie ein, dass Ihnen die LUMITOS AG den oder die oben ausgewählten Newsletter per E-Mail zusendet. Ihre Daten werden nicht an Dritte weitergegeben. Die Speicherung und Verarbeitung Ihrer Daten durch die LUMITOS AG erfolgt auf Basis unserer Datenschutzerklärung. LUMITOS darf Sie zum Zwecke der Werbung oder der Markt- und Meinungsforschung per E-Mail kontaktieren. Ihre Einwilligung können Sie jederzeit ohne Angabe von Gründen gegenüber der LUMITOS AG, Ernst-Augustin-Str. 2, 12489 Berlin oder per E-Mail unter widerruf@lumitos.com mit Wirkung für die Zukunft widerrufen. Zudem ist in jeder E-Mail ein Link zur Abbestellung des entsprechenden Newsletters enthalten.