Neue Dünnschicht-Elektroden aus Silizium und Lithium für die »Forschungsfabrik Batterie«
Bessere Batterien für Elektroautos »Made in Germany«
Deutsche Wissenschaftler wollen im Dachkonzept »Forschungsfabrik Batterie« neuartige Batterien entwickeln, die bei gleichem Volumen mindestens 70 Prozent mehr Energie für Elektrofahrzeuge und Smartphones speichern können als herkömmliche Lithium-Ionen-Lösungen. Im Rahmen des vom Bundesministerium für Bildung und Forschung (BMBF) geförderten Kompetenzclusters für Batteriematerialien »ExcellBattMat« steuert das Dresdner »ExcellBattMat-Zentrum« (Projekt KaSiLi: Strukturmechanische Kathodenadaption für Silizium- und Lithiumwerkstoffe) Schlüsselkomponenten für diese neue Batterie-Generation bei. Die Forscher von Fraunhofer, TU-Dresden und Leibniz arbeiten seit dem 1. November 2019 gemeinsam an innovativen Batterie-Elektroden, die aus hauchdünnen Silizium- oder Lithiumschichten bestehen, um hohe Energiedichten zu erreichen.

REM-Aufnahme einer Siliziumschicht mit definierter Struktur. Über die gezielte Einstellung von Struktur und Dicke der Schichten lassen sich die Eigenschaften der Anoden in der Batterieanwendung steuern.
© Fraunhofer IWS Dresden
Elektrofahrzeuge sollen mit einer Batterieladung bis zu 700 Kilometer weit fahren, Smartphones deutlich seltener aufgeladen werden. Dafür wird »KaSiLi« stehen, das von Dresden aus unter der Federführung des Fraunhofer Instituts für Werkstoff- und Strahltechnik IWS im Verbund drei Jahre lang an neuen Elektroden-Technologien forschen soll. »Dadurch bahnt sich ein Quantensprung für die Batterietechnik an«, hofft Prof. Christoph Leyens, Institutsleiter des Fraunhofer IWS und Direktor des Instituts für Werkstoffwissenschaft der Technischen Universität Dresden. »Diese disruptive Technologie hat das Potenzial, den Standort Deutschland deutlich voranzubringen«, meint auch Chemie-Professor Stefan Kaskel von der TU Dresden, der in Personalunion das »ExcellBattMat-Zentrum« (kurz: EBZ) am Fraunhofer IWS und das vom BMBF geförderte KaSiLi-Projekt leitet.
Expertise für eine elektromobile Zukunft
In der langen Wertschöpfungskette von der Batteriezelle bis zum fertigen Elektroauto könne die deutsche Wirtschaft so deutlich an Gewicht gewinnen. »Letztlich wollen wir eine moderne Batteriezellen-Produktion in Deutschland etablieren. Dadurch wären wir bei der Wende hin zu Elektromobilität und zu erneuerbaren Energien weniger als bisher von Zulieferungen aus Fernost oder den USA abhängig«, betont Kaskel. Um dies zu erreichen, entwickeln die Dresdner neue Materialien, Designprinzipien und Verarbeitungstechnologien für die Elektroden in den kleinsten Energiespeicher-Einheiten eines Akkumulators, die heute meist als Batteriezellen bezeichnet werden. Wichtige Bauteile in solch einer Zelle sind Anode und Kathode. Zwischen diesen beiden Polen wandern die elektrischen Ladungsträger hin und her, wenn eine Batterie geladen wird oder wenn sie gerade Strom für den Elektromotor in einem E-Auto liefert. Heute besteht die Anode in einer Lithium-Ionen-Batterie meist aus einem wenige Mikrometer (Tausendstel Millimeter) dünnen Kupfer-Stromleiter, der mit einer etwa 100 Mikrometer dicken Grafitschicht bedeckt ist.
Energiedichten von über 1.000 Wattstunden je Liter erreichbar
Diese Graphit-Schicht wollen die Dresdner Chemiker durch weit dünnere Schichten aus Silizium oder Lithium ersetzen. Diese sollen dann nur noch rund zehn bis 20 bis 30 Mikrometer messen. Im Labor funktioniert das auch schon recht gut und sorgt bereits für mehr Energiespeicher-Vermögen. »Heutige Lithium-Ionen-Akkus kommen auf eine Energiedichte von etwa 240 Wattstunden pro Kilogramm bzw. bis 670 Wattstunden pro Liter«, erklärt Stefan Kaskel. »Mit unseren Elektroden wollen wir auf deutlich über 1.000 Wattstunden pro Liter kommen«.
Auf dem Weg dahin müssen die Entwickler allerdings nicht nur die Chemie und die Beschichtungsprozesse für ihre Zellen weiter verbessern, sondern auch ein mechanisches Problem lösen: Unter dem Mikroskop hat sich gezeigt, dass die mit Silizium oder Lithium dünn beschichteten Elektroden immer wieder schrumpfen und sich ausdehnen, wenn die Batterien aufgeladen oder entladen werden – als ob die Zelle atmen würde. Dies ist allerdings ein Problem, da die mechanische Belastung die Elektroden durch diese »Atmung« rasch zerstören kann. Daher experimentieren die Kooperationspartner nun auch mit winzig kleinen Federn. Dafür arbeiten sie an speziellen Schichten für die Kathode: »Durch eine spezielle Anpassung ihrer mikroskopischen Eigenschaften soll diese abfedernde Eigenschaften erhalten und damit ebenfalls wesentlich zu einer höheren Energiedichte der neuen Batteriegeneration beitragen«, so Dr. Kristian Nikolowski vom Fraunhofer-Institut für Keramische Technologen und Systeme IKTS.
Partner von Fraunhofer, TU und Leibniz ziehen in Dresden an einem Strang
Um all diese Technologien in Prototypen zu gießen und schließlich zur Serienreife zu führen, vereinen die KaSiLi-Partner verschiedene Forschungsstärken, die einander ergänzen. Das IWS bringt seine Erfahrungen in der Dünnschicht-Technologie ein. Das Fraunhofer IKTS kümmert sich um die oxidische Kathodentechnik und deren Skalierung. Das Nanoelektronik-Labor »NaMLab« der Technischen Universität Dresden (TUD) untersucht mit speziellen Spektroskopie-Anlagen die neudesignten Anoden. Das Leibniz-Institut für Festkörper- und Werkstoffforschung (IFW) Dresden fokussiert sich auf die strukturellen Analysen der Elektrodenschichten. Die TUD-Lehrstühle für anorganische Chemie von Prof. Stefan Kaskel und für anorganisch-nichtmetallische Werkstoffe von Prof. Alexander Michaelis übernehmen die Vorlaufforschung für neue Elektroden-Aufbauten.
Außerdem kooperieren diese Dresdner Institute mit den drei anderen ExcellBattMat-Zentren Deutschlands aus Münster, München und Ulm. Die Dresdner Forscher agieren dabei als eine Art Hightech-Schmiede für neue Werkstoffe innerhalb des deutschlandweiten Dachkonzepts »Forschungsfabrik Batterie«, das zahlreiche Batterie-Förderaktivitäten des BMBFs unter einem Dach vereint.
Prototypen für Forschungsfertigung in Münster sollen 2022 fertig sein
Bis zum Jahr 2022 wollen die KaSiLi-Partner funktionsfähige Demonstratoren fertig haben. Danach fließt das neue Batterie-Design in eine »Forschungsfertigung Batteriezelle« in Münster ein. All dies zielt letztlich darauf, eine eigene Großproduktion von Batteriezellen in der Bundesrepublik aufzubauen. Dies soll die Wettbewerbsfähigkeit von Elektroautos »Made in Germany« verbessern und Arbeitsplätze in Deutschland sichern.
Weitere News aus dem Ressort Wissenschaft
Meistgelesene News
Weitere News von unseren anderen Portalen
Verwandte Inhalte finden Sie in den Themenwelten
Themenwelt Batterietechnik
Die Themenwelt Batterietechnik bündelt relevantes Wissen in einzigartiger Weise. Hier finden Sie alles über Anbieter und deren Produkte, Webinare, Whitepaper, Kataloge und Broschüren.
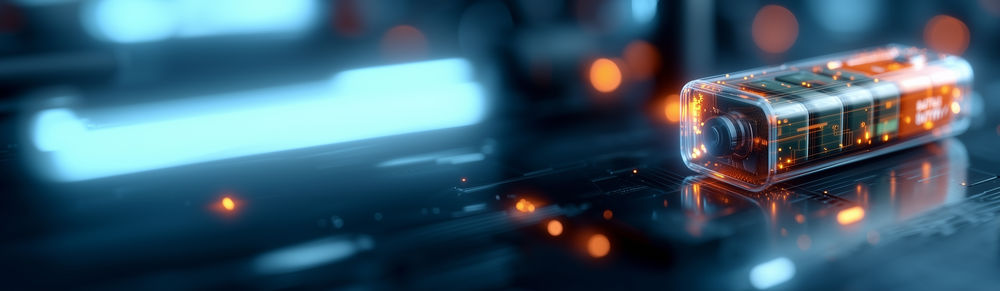
Themenwelt Batterietechnik
Die Themenwelt Batterietechnik bündelt relevantes Wissen in einzigartiger Weise. Hier finden Sie alles über Anbieter und deren Produkte, Webinare, Whitepaper, Kataloge und Broschüren.