Algorithmus lernt, 3D-Druckfehler für verschiedene Teile, Materialien und Systeme zu korrigieren
Spin-Out-Unternehmen gegründet
Ingenieure haben intelligente 3D-Drucker entwickelt, die Fehler schnell erkennen und korrigieren können, selbst bei bisher unbekannten Designs oder unbekannten Materialien wie Ketchup und Mayonnaise, indem sie aus den Erfahrungen anderer Maschinen lernen.
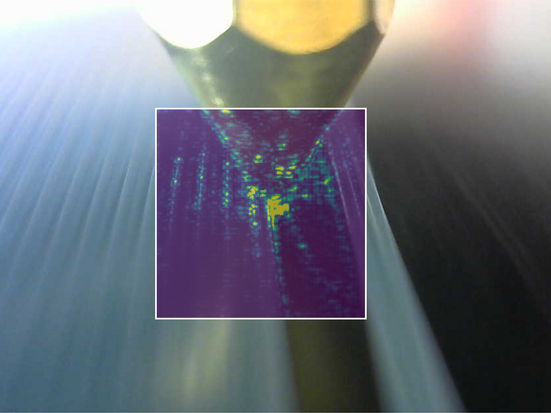
Beispielbild der Düse eines 3D-Druckers, das von einem Algorithmus für maschinelles Lernen zur Erkennung und Korrektur von Fehlern in Echtzeit verwendet wird. Hervorgehobene Bereiche zeigen Aspekte des Bildes, auf die sich das System konzentriert, und geben potenzielle Einblicke in die Art und Weise, wie der Algorithmus Vorhersagen trifft.
Douglas Brion
Die Ingenieure der Universität Cambridge haben einen Algorithmus für maschinelles Lernen entwickelt, der eine Vielzahl von Fehlern in Echtzeit erkennen und korrigieren kann und sich leicht in neue oder bestehende Maschinen einbauen lässt, um deren Fähigkeiten zu verbessern. 3D-Drucker, die den Algorithmus verwenden, könnten auch selbst lernen, wie sie neue Materialien drucken können. Einzelheiten zu ihrem kostengünstigen Ansatz sind in der Zeitschrift Nature Communications veröffentlicht.
Der 3D-Druck hat das Potenzial, die Herstellung komplexer und individueller Teile wie Flugzeugkomponenten, personalisierter medizinischer Implantate oder sogar komplizierter Süßigkeiten zu revolutionieren, und könnte auch die Produktionslieferketten verändern. Allerdings ist sie auch anfällig für Produktionsfehler, von kleinen Ungenauigkeiten und mechanischen Schwächen bis hin zu Totalausfällen.
Derzeit besteht die Möglichkeit, diese Fehler zu vermeiden oder zu korrigieren, darin, dass ein Facharbeiter den Prozess beobachtet. Der Mitarbeiter muss einen Fehler erkennen (was selbst für ein geschultes Auge eine Herausforderung ist), den Druckvorgang anhalten, das Teil entfernen und die Einstellungen für ein neues Teil anpassen. Wird ein neues Material oder ein neuer Drucker verwendet, nimmt der Prozess mehr Zeit in Anspruch, da der Mitarbeiter die neuen Einstellungen erlernen muss. Selbst dann können Fehler übersehen werden, da die Mitarbeiter nicht ständig mehrere Drucker gleichzeitig beobachten können, insbesondere bei langen Druckvorgängen.
"3D-Druck ist eine Herausforderung, denn es kann viel schief gehen, und so kommt es häufig vor, dass 3D-Drucke scheitern", sagt Dr. Sebastian Pattinson vom Cambridge Department of Engineering, der Erstautor der Studie. "Wenn das passiert, ist das gesamte Material, die Zeit und die Energie, die man verbraucht hat, verloren".
Ingenieure haben eine automatisierte 3D-Drucküberwachung entwickelt, aber die bestehenden Systeme können nur eine begrenzte Anzahl von Fehlern bei einem Teil, einem Material und einem Drucksystem erkennen.
"Was wir wirklich brauchen, ist ein 'fahrerloses Auto'-System für den 3D-Druck", sagt Erstautor Douglas Brion, ebenfalls vom Fachbereich Ingenieurwesen. "Ein fahrerloses Auto wäre nutzlos, wenn es nur auf einer Straße oder in einer Stadt funktionieren würde - es muss lernen, sich in verschiedenen Umgebungen, Städten und sogar Ländern zurechtzufinden. In ähnlicher Weise muss ein 'fahrerloser' Drucker für verschiedene Teile, Materialien und Druckbedingungen funktionieren."
Brion und Pattinson sagen, dass der von ihnen entwickelte Algorithmus das "fahrerlose Auto" sein könnte, nach dem die Ingenieure gesucht haben.
"Das bedeutet, dass man einen Algorithmus haben könnte, der alle verschiedenen Drucker, die man betreibt, ständig überwacht und bei Bedarf Änderungen vornimmt - im Grunde das tut, was ein Mensch nicht tun kann", so Pattinson.
Die Forscher trainierten ein Deep-Learning-Computer-Vision-Modell, indem sie ihm rund 950.000 Bilder vorlegten, die während der Produktion von 192 gedruckten Objekten automatisch aufgenommen wurden. Jedes der Bilder wurde mit den Einstellungen des Druckers versehen, wie Geschwindigkeit und Temperatur der Druckdüse und Durchflussmenge des Druckmaterials. Das Modell erhielt auch Informationen darüber, wie weit diese Einstellungen von guten Werten entfernt waren, so dass der Algorithmus lernen konnte, wie Fehler entstehen.
"Sobald der Algorithmus trainiert ist, kann er allein durch das Betrachten eines Bildes herausfinden, welche Einstellung richtig und welche falsch ist - ist eine bestimmte Einstellung beispielsweise zu hoch oder zu niedrig - und dann die entsprechende Korrektur vornehmen", so Pattinson. "Und das Tolle daran ist, dass Drucker, die diesen Ansatz verwenden, kontinuierlich Daten sammeln können, so dass der Algorithmus auch kontinuierlich verbessert werden kann."
Mit diesem Ansatz konnten Brion und Pattinson einen Algorithmus entwickeln, der verallgemeinerbar ist, d. h. er kann zur Erkennung und Korrektur von Fehlern bei unbekannten Objekten oder Materialien oder sogar bei neuen Drucksystemen eingesetzt werden.
"Wenn man mit einer Düse druckt, kann es unabhängig vom verwendeten Material - Polymere, Beton, Ketchup oder was auch immer - zu ähnlichen Fehlern kommen", so Brion. "Wenn sich die Düse zum Beispiel zu schnell bewegt, entstehen oft Materialkleckse, oder wenn man zu viel Material ausstößt, überlappen sich die gedruckten Linien und bilden Falten.
"Fehler, die durch ähnliche Einstellungen entstehen, weisen ähnliche Merkmale auf, unabhängig davon, welches Teil gedruckt wird oder welches Material verwendet wird. Da unser Algorithmus allgemeine Merkmale erlernt hat, die für verschiedene Materialien gelten, konnte er sagen: 'Oh, die gedruckten Linien bilden Falten, also haben wir wahrscheinlich zu viel Material herausgedrückt'."
So konnte der Algorithmus, der nur mit einer Art von Material und Drucksystem trainiert wurde, Fehler bei verschiedenen Materialien, von technischen Polymeren bis hin zu Ketchup und Mayonnaise, auf einem anderen Drucksystem erkennen und korrigieren.
In Zukunft könnte der trainierte Algorithmus bei der Erkennung von Fehlern effizienter und zuverlässiger sein als ein menschlicher Bediener. Dies könnte für die Qualitätskontrolle bei Anwendungen wichtig sein, bei denen das Versagen von Komponenten schwerwiegende Folgen haben könnte.
Mit Unterstützung von Cambridge Enterprise, dem Kommerzialisierungszweig der Universität, hat Brion das Spin-Out-Unternehmen Matta gegründet, das die Technologie für kommerzielle Anwendungen entwickeln soll.
"Wir konzentrieren uns darauf, wie dies in hochwertigen Branchen wie der Luft- und Raumfahrt, dem Energiesektor und der Automobilindustrie funktionieren könnte, wo 3D-Drucktechnologien zur Herstellung von leistungsstarken und teuren Teilen eingesetzt werden", so Brion. "Es kann Tage oder Wochen dauern, bis ein einzelnes Bauteil fertiggestellt ist, dessen Kosten sich auf mehrere tausend Pfund belaufen. Ein Fehler, der am Anfang auftritt, wird möglicherweise erst entdeckt, wenn das Teil fertiggestellt und geprüft ist. Unser Ansatz würde den Fehler in Echtzeit erkennen und die Produktivität der Fertigung erheblich verbessern."
Hinweis: Dieser Artikel wurde mit einem Computersystem ohne menschlichen Eingriff übersetzt. LUMITOS bietet diese automatischen Übersetzungen an, um eine größere Bandbreite an aktuellen Nachrichten zu präsentieren. Da dieser Artikel mit automatischer Übersetzung übersetzt wurde, ist es möglich, dass er Fehler im Vokabular, in der Syntax oder in der Grammatik enthält. Den ursprünglichen Artikel in Englisch finden Sie hier.
Originalveröffentlichung
Weitere News aus dem Ressort Wissenschaft
Diese Produkte könnten Sie interessieren
Meistgelesene News
Weitere News von unseren anderen Portalen
Da tut sich was in der Chemie-Branche …
So sieht echter Pioniergeist aus: Jede Menge innovative Start-ups bringen frische Ideen, Herzblut und Unternehmergeist auf, um die Welt von morgen zum Positiven zu verändern. Tauchen Sie ein in die Welt dieser Jungunternehmen und nutzen Sie die Möglichkeit zur Kontaktaufnahme mit den Gründern.